TRIR – The higher than usual occurrence of injuries in 2023 was mainly derived of a new production line at one of our sites, installed in mid-2023. Following safety incidents related to the line, the site Safety Officer and our Global EHS Director launched a thorough investigation and root cause analysis, revealing safety hazards in specific locations along this new line, which was delivering larger and heavier products than previously produced at this site. Corrective actions were implemented, including both physical alterations to the production line itself and amendments to the work procedures. Injuries and investigation findings were reported to the CEO and executive management.
LTIR – During 2023, two specific injuries at two different sites resulted in long-term loss of work (over 100 days each). One of these injuries was experienced by a newly recruited employee and is currently under investigation to determine if it’s severity could be related to a pre-existing condition.
Safety performance: The overall Total Recordable Incident Rate (TRIR) for our global employees in 2023 was 0.66. This rate falls within our continuous overall target of an annual TRIR rate that does not exceed 0.7, yet still constitutes a 9% increase from the 2022 TRIR of 0.61. In parallel, our global Lost Time Incident Rate due to safety incidents (LITR) increased from 11.0 in 2022 to 17.9 in 2023 (+63%).
Following are explanations for these trends:
Sustainability Report 2023 /
Health & Safety
LTIR Rate - Global Company Employees
11.9
60
11.0
17.9
2023
2022
2021
TRIR Rate - Global Company Employees
0.50
60
0.61
0.66
2023
2022
2021
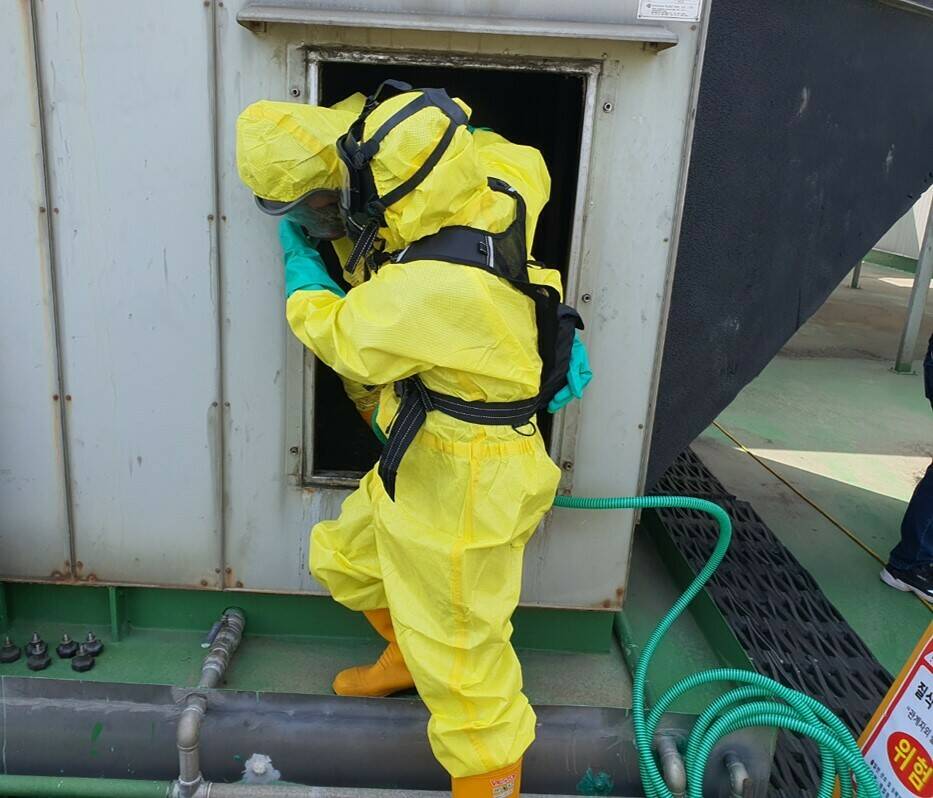
hours of safety training,
averaging over
3.7
28,000
annual training hours per employee.
In 2023, SolarEdge employees participated in more than
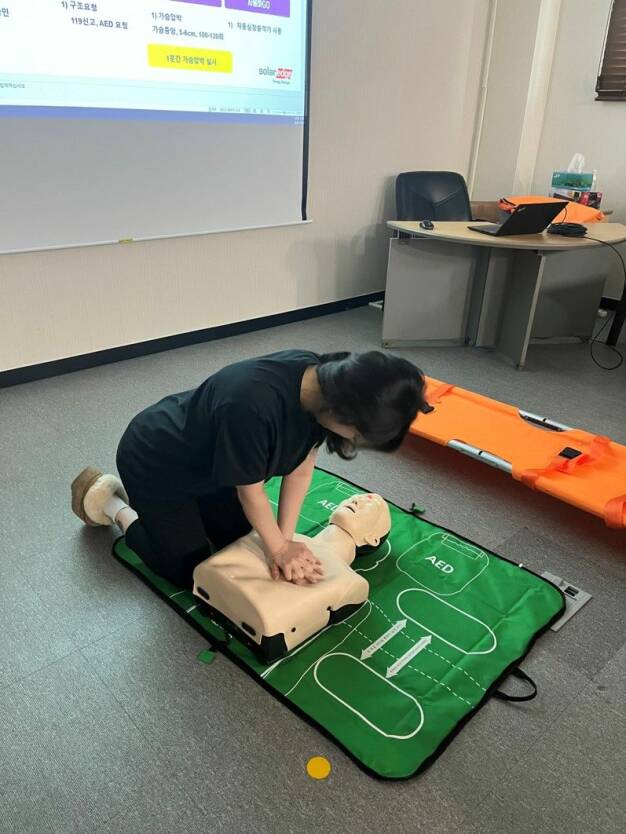
Site-specific risk analysis evaluates the potential impact of operational tasks or conditions on employee health and safety. Common topics covered in the risk analysis include fires, use of hazardous substances, electrocution, slips, trips, falls, noise, electromagnetic work, ergonomics, and waste management. We work to mitigate all identified risks or hazards by putting processes and procedures in place that reduce the likelihood of their occurrence, in addition to assigning specific personnel with responsibility for risk mitigation, and setting a defined timeline for required corrective actions.
Safety Management Plans: Each of our operational sites maintains a site-specific safety management plan, prepared according to local regulations and approved by the site EHS Manager/Safety Officer. These plans include elements such as:
Safety goals and KPIs
Establishing roles and responsibilities regarding day-to-day safety as well as emergency events
Site-specific directions on health and safety training
Safety procedures regarding work with external contractors
Procedures regarding periodic tests for equipment and materials
Guidelines for conducting annual site-specific health and safety risk analysis (see below).
An EHS regulatory and compliance monitoring system, tracking relevant global regulations, and assisting with customized audit planning.
An incident reporting and investigation system for our Israeli sites, aimed at methodically finding the incident’s root cause and helping with risk elimination; and
Training management to better track training obligations and the progress of our expanding global workforce
Safety enhancing tools and systems: In recent years, we have implemented systems for tracking global EHS performance, aimed to help reduce safety risks and support ongoing EHS compliance worldwide. These systems include:
Safety training: The vast majority of our global workforce undergo annual mandatory safety training. The remainder of the workforce receive periodic safety training, in accordance with local regulations.
Our 2023 safety training included a specific focus on electrical safety, including an electrical safety campaign specifically designed for our R&D sites. Additional focus areas included enhanced fire prevention, expanded first aid training, and emergency response training (among other topics, risks associated with Li-Ion battery production and handling).
Our health and safety practices include:
Nominated Safety Officers at each company manufacturing/R&D site. Our Safety Officers have gained specific expertise in the processes and technologies that characterize SolarEdge’s activities.
Nominated lab electricity supervising engineers in two main R&D sites, focusing specifically on prevention of electricity-related incidents.
Appointed and trained employees in each manufacturing/R&D site as Safety Trustees who help enhance their site’s local safety culture.
Mandatory job-specific training (such as proper use of protective equipment, working with high voltage, working in heights, safe use of machinery/chemicals/materials, etc.) for all employees in relevant roles.
Comprehensive safety, fire, and emergency drill programs to ensure employees are well-versed with emergency procedures.
Root-cause assessments of incidents and corrective actions.
Conducting periodic internal and external EHS audits within the company and at contract manufacturer sites.
Supplying employees with all necessary PPE (Personal Protective Equipment) according to the identified job-specific risks and all relevant regulations.
Maintaining a healthy and ergonomic work environment. Provide employees with specialized ergonomic equipment when reasonably required/requested.
Extensive safety training (details below).
Overall accountability for safety at SolarEdge rests with the Vice President of Quality & Reliability (Q&R), a member of our executive management team. The SolarEdge Global EHS Director reports to the VP Q&R and manages all aspects of safety and environmental compliance and improvement. Safety performance is reported monthly to the company Chief Executive Officer and executive management, including specific safety incidents analysis, findings, corrective actions and updates on safety improvements.
We believe that all accidents and injuries at work are preventable, and we strive to achieve a zero-injury culture across our offices and operations. We comply with applicable occupational health and safety regulations. All SolarEdge manufacturing and R&D sites are certified to Occupational Health and Safety Quality Management Standard ISO 45001:2018.
Join the SolarEdge Conversation
Contact our sustainability / ESG team
Contact us
How can we help you?
Join the SolarEdge Conversation
Contact our sustainability / ESG team
Contact us
How can we help you?
Site-specific risk analysis evaluates the potential impact of operational tasks or conditions on employee health and safety. Common topics covered in the risk analysis include fires, use of hazardous substances, electrocution, slips, trips, falls, noise, electromagnetic work, ergonomics, and waste management. We work to mitigate all identified risks or hazards by putting processes and procedures in place that reduce the likelihood of their occurrence, in addition to assigning specific personnel with responsibility for risk mitigation, and setting a defined timeline for required corrective actions.
Safety goals and KPIs
Establishing roles and responsibilities regarding day-to-day safety as well as emergency events
Site-specific directions on health and safety training
Safety procedures regarding work with external contractors
Procedures regarding periodic tests for equipment and materials
Guidelines for conducting annual site-specific health and safety risk analysis (see below).
Safety Management Plans: Each of our operational sites maintains a site-specific safety management plan, prepared according to local regulations and approved by the site EHS Manager/Safety Officer. These plans include elements such as:
Safety enhancing tools and systems: In recent years, we have implemented systems for tracking global EHS performance, aimed to help reduce safety risks and support ongoing EHS compliance worldwide. These systems include:
An EHS regulatory and compliance monitoring system, tracking relevant global regulations, and assisting with customized audit planning.
An incident reporting and investigation system for our Israeli sites, aimed at methodically finding the incident’s root cause and helping with risk elimination; and
Training management to better track training obligations and the progress of our expanding global workforce
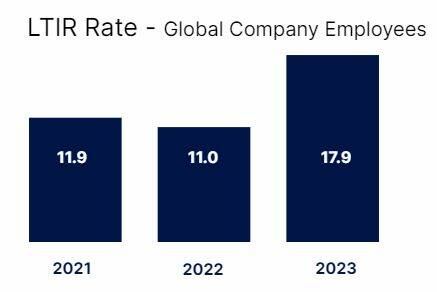
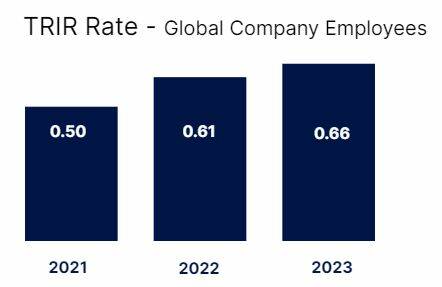
3.7
annual training hours per employee.
hours of safety training,
averaging over
28,000
In 2023, SolarEdge employees participated in more than
Safety training: The vast majority of our global workforce undergo annual mandatory safety training. The remainder of the workforce receive periodic safety training, in accordance with local regulations.
Our 2023 safety training included a specific focus on electrical safety, including an electrical safety campaign specifically designed for our R&D sites. Additional focus areas included enhanced fire prevention, expanded first aid training, and emergency response training (among other topics, risks associated with Li-Ion battery production and handling).
TRIR – The higher than usual occurrence of injuries in 2023 was mainly derived of a new production line at one of our sites, installed in mid-2023. Following safety incidents related to the line, the site Safety Officer and our Global EHS Director launched a thorough investigation and root cause analysis, revealing safety hazards in specific locations along this new line, which was delivering larger and heavier products than previously produced at this site. Corrective actions were implemented, including both physical alterations to the production line itself and amendments to the work procedures. Injuries and investigation findings were reported to the CEO and executive management.
LTIR – During 2023, two specific injuries at two different sites resulted in long-term loss of work (over 100 days each). One of these injuries was experienced by a newly recruited employee and is currently under investigation to determine if it’s severity could be related to a pre-existing condition.
Safety performance: The overall Total Recordable Incident Rate (TRIR) for our global employees in 2023 was 0.66. This rate falls within our continuous overall target of an annual TRIR rate that does not exceed 0.7, yet still constitutes a 9% increase from the 2022 TRIR of 0.61. In parallel, our global Lost Time Incident Rate due to safety incidents (LITR) increased from 11.0 in 2022 to 17.9 in 2023 (+63%).
Following are explanations for these trends:
Nominated Safety Officers at each company manufacturing/R&D site. Our Safety Officers have gained specific expertise in the processes and technologies that characterize SolarEdge’s activities.
Nominated lab electricity supervising engineers in two main R&D sites, focusing specifically on prevention of electricity-related incidents.
Appointed and trained employees in each manufacturing/R&D site as Safety Trustees who help enhance their site’s local safety culture.
Mandatory job-specific training (such as proper use of protective equipment, working with high voltage, working in heights, safe use of machinery/chemicals/materials, etc.) for all employees in relevant roles.
Comprehensive safety, fire, and emergency drill programs to ensure employees are well-versed with emergency procedures.
Root-cause assessments of incidents and corrective actions.
Conducting periodic internal and external EHS audits within the company and at contract manufacturer sites.
Supplying employees with all necessary PPE (Personal Protective Equipment) according to the identified job-specific risks and all relevant regulations.
Maintaining a healthy and ergonomic work environment. Provide employees with specialized ergonomic equipment when reasonably required/requested.
Extensive safety training (details below).
Our health and safety practices include:
Overall accountability for safety at SolarEdge rests with the Vice President of Quality & Reliability (Q&R), a member of our executive management team. The SolarEdge Global EHS Director reports to the VP Q&R and manages all aspects of safety and environmental compliance and improvement. Safety performance is reported monthly to the company Chief Executive Officer and executive management, including specific safety incidents analysis, findings, corrective actions and updates on safety improvements.
We believe that all accidents and injuries at work are preventable, and we strive to achieve a zero-injury culture across our offices and operations. We comply with applicable occupational health and safety regulations. All SolarEdge manufacturing and R&D sites are certified to Occupational Health and Safety Quality Management Standard ISO 45001:2018.