Join the SolarEdge Conversation
Contact our sustainability / ESG team
Contact us
How can we help you?
Reducing a PV system’s DC voltage to a safe level when the system is shut down
Designing for early fault detection
Applying active and continuous protection mechanisms
Supporting module-level monitoring with actionable fault alerts
Allowing conductors to rapidly discharge their electric load down to safe voltage levels
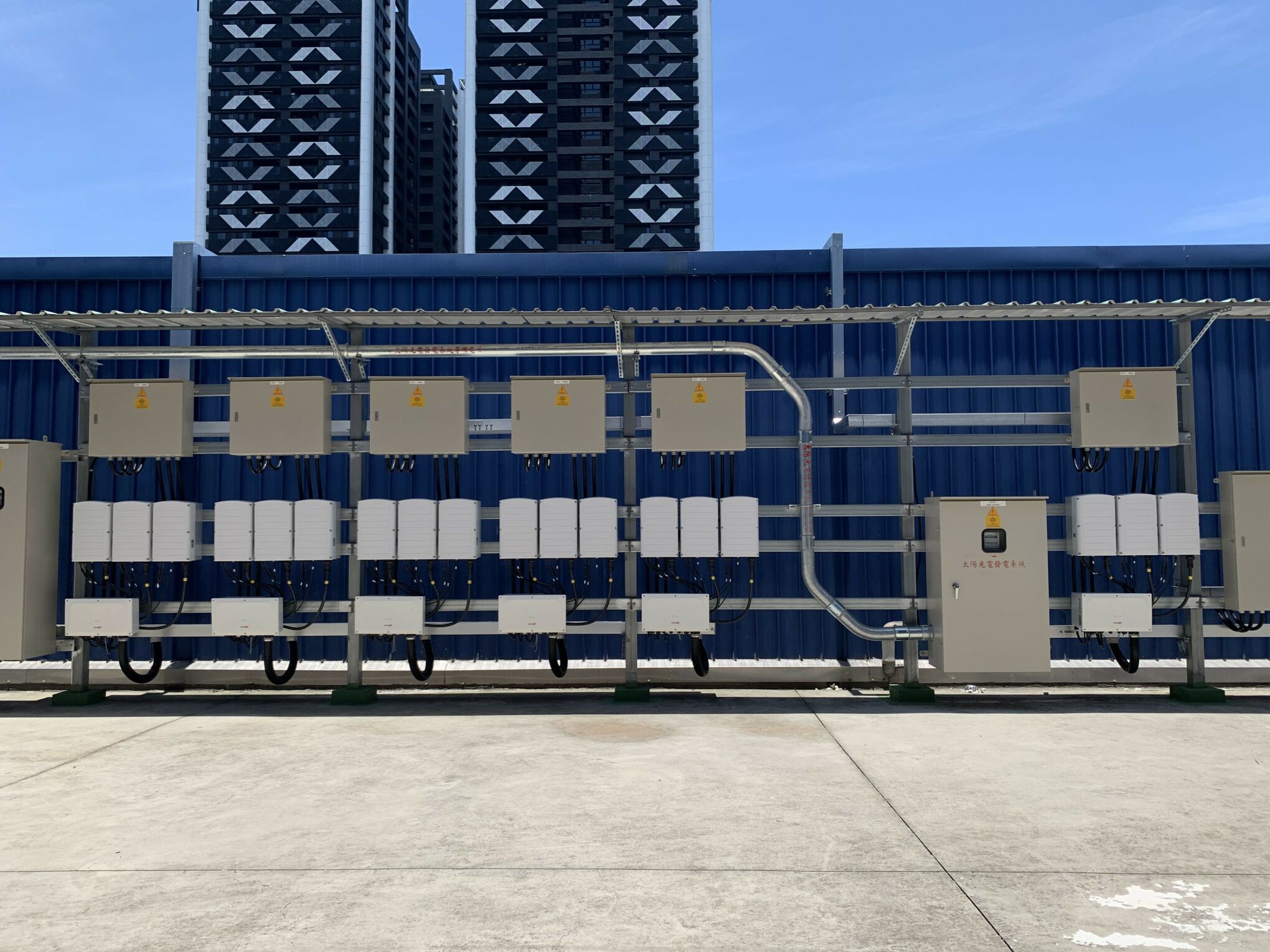
A key element of our integrated safety system is our SafeDC™ built-in proprietary safety technology. This feature is designed to minimize the risk of electrocution from high DC voltage. Upon activation of SafeDC™, our Power Optimizers automatically revert to their default touch-safe voltage of only 1V in less than one minute. SafeDC™ is activated in the following cases: during installation, when strings are disconnected from the inverter; when the inverter is turned off, locked or disabled; or when AC connection is shut down. The SafeDC™ feature helps to protect people engaged in PV system inspection and maintenance activities, as well as enabling emergency responders to address fires in homes or other buildings with confidence that the system does not pose an additional hazard.
Our monitoring abilities are another core part of our holistic safety management system. SolarEdge’s platform provides continuous remote monitoring at the module, string, and system level, allowing for greater visibility of system performance. The platform’s automatic alerts are designed to provide accurate and immediate fault detection, allowing for better hazard recognition and rapid response in case of product safety incidents.
An additional important safety feature of our systems is our advanced electric arc detection and prevention mechanism, already operated in many of our installed and monitored SolarEdge PV systems. An electric arc is an unintended, prolonged electrical discharge occurring across a small air gap. Since photovoltaic systems have many connection points, arc faults can occur, causing potential fire hazards. SolarEdge has developed state-of-the-art arc fault detection algorithms and AFCI (Arc Fault Circuit Interruption) mechanisms. These algorithms are designed to locate potential arc faults and to prevent them through corrective actions and are available for implementation on more than a million of our inverters. The algorithms were tested by certification entities and third-party companies to ensure that they pass the set requirements and provide the expected performance, under a full range of electrical conditions and various types of installations.
A prominent example of these mechanisms is the SolarEdge Sense Connect feature included in the new S-Series Power Optimizers. SolarEdge Sense Connect is an industry-first technology that detects temperature increase at the connector level, stopping power flow before an arc can occur.
We dedicate significant resources to widespread safety training, focusing on potential risks related to our business and products, such as electrification, fire and working on roofs. This training is conducted both for our employees (see “Health & Safety”) and our global community of installers (see “Customer Service”).
At SolarEdge, safety is a primary feature of all our product offerings, and is a key element of our product design, development and testing. Similarly, as an industry leader in technologies that promote environmentally friendly solutions for energy generation, we strive to minimize the footprint of our value chain as much as possible.
We build our products for lasting performance, offering extensive warranties for Power Optimizers and inverters, so customers can benefit from highly efficient clean energy without wasting resources on replacement units. To further reduce waste and material usage, we also refurbish products - in cases where it is possible and viable (see “Refurbishing” above). We also work to ensure the recyclability of our products when they reach their eventual end-of-life stages. See full details in section “Waste Management”.
We help in securing a sustainable end-of-life for our products by participating in regulatory schemes mandated in some regions where we operate, in which manufacturers and importers of electronic equipment and batteries pay levies aimed to fund the eventual collection and recycling of their sold products, at their eventual end-of-life. Such schemes include the EU “Take Back” program of the Waste Electrical and Electronic Equipment (WEEE) directive, and other similar country-specific regulations.
We’ve instituted a useful procedure for waste recovery at some of our sites, including Sella 1 in Israel as an example. Non-household waste including hazardous waste, carboard, and scrap metal and e-waste is separated at the source and sent for external recycling at licensed facilities. This eases the later external process of recycling.
Recently, storage solutions have been forming an increasing part of SolarEdge’s activities, offerings and revenues. In parallel, the Company has experienced growing interest from stakeholders regarding the challenging global issues of battery end-of-life. In the cases of batteries that have experienced defaults, the batteries will often undergo a refurbishing process at SolarEdge designated sites (see above). These batteries can often be refurbished and reused (especially when the fault is an issue with electronic components). We began working with battery recycling sites in several locations in order to handle remaining batteries that cannot be repaired). We continue to examine potential approaches and solutions to mitigate this issue.
Product End-of-Life
In recent years, the packaging design process for new SolarEdge products focused on finding cost-effective packaging molds that could be made from recyclable materials while fully protecting our products from harm during shipment. Wherever such reasonable options were found, the company designed, and is now using, recyclable packaging materials such as cardboard, pulp and wood. Our Power Optimizers, batteries, and some additional products, are now delivered in packaging made from these recyclable materials. We continue to search for recyclable packaging options for our other products as well, striving to meet both physical and reasonable cost criteria. In parallel, we are monitoring evolving regulations on packaging materials in different global regions to ensure our current and future compliance.
Sustainable Packaging
Our products are built durably, for the long term and come with an extensive warranty. However, if one of our inverters or batteries nonetheless exhibits a malfunction that cannot be repaired on-site or remotely within the warranty period, it is replaced by the Company. SolarEdge inverters and batteries that need to be replaced are often sent to our refurbishing sites in Europe and the U.S. where Company refurbishing experts examine the malfunction, change electronic or other components as required, conduct quality tests (similar to those that new products are put through), and package the refurbished products as viable replacements. The refurbishing process and expertise provide both a cost-saving benefit for the company and a circularity environmental value. The process reduces some of the need for new electronic components, as well as the costs and environmental impact associated with shipping by partially reducing overseas delivery of new products. Malfunctioned products that cannot be refurbished, are often recycled (see “Product End-of-Life” below).
Refurbishing
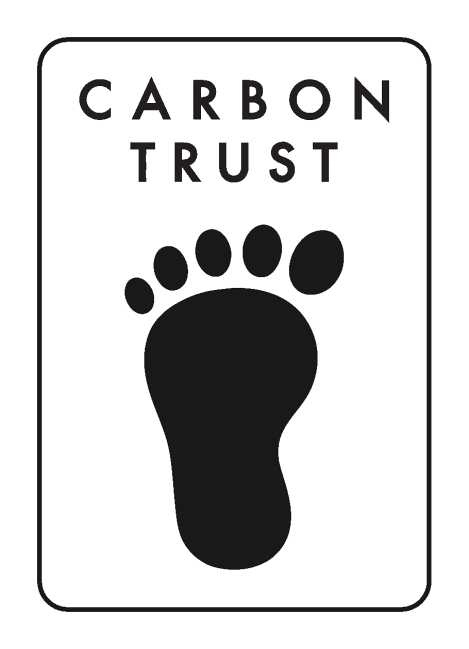
SolarEdge solutions support the worldwide transition to renewable, low-carbon power generation and consumption. The use of our systems allows for millions of tonnes of GHG emissions to be avoided each year. We also strive to examine and reduce the carbon emissions related to the sourcing, production and shipping of our products.
As part of these efforts, we conducted a comprehensive carbon footprint analysis for leading models of our inverters and Power Optimizers. The analysis process was led and certified by carbon footprint and decarbonization experts, Carbon Trust. The analysis allows us to understand the main emission sources throughout our products’ lifecycle, helping us better understand our emission reduction opportunities. We are currently working on the expansion of our LCA analysis scope for several additional products and additional environmental impacts and aim to complete this expanded process during 2024.
Lifecycle Assessment
SolarEdge complies with the following international standards and with various environmental regulations:
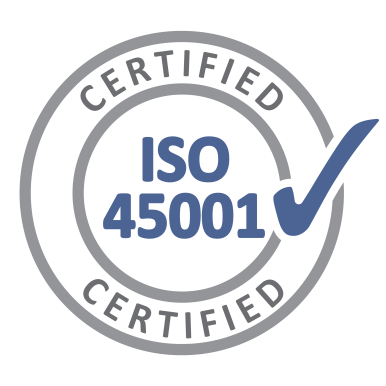
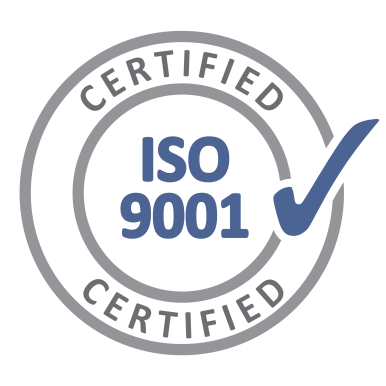
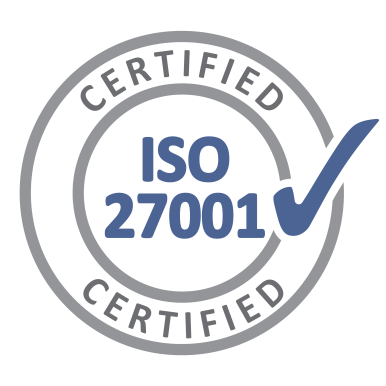
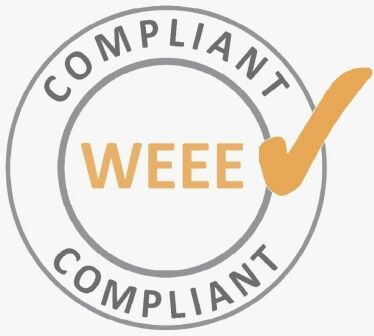
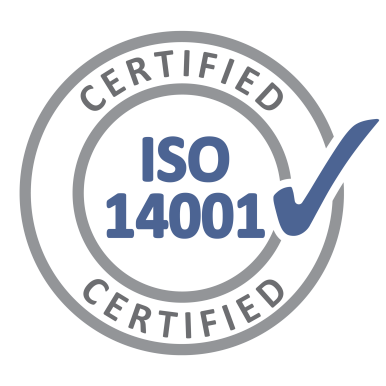
We continuously act to certify all the manufacturing and R&D sites under our operational control according to relevant ISO standards for management systems in the fields of quality, environment and safety. By the end of 2023, 100% of the designated sites in all relevant countries (Israel, South-Korea, Italy and the US) were certified to ISO 9001 (quality), ISO 14001 (environmental management) and ISO 45001 (safety management).
All SolarEdge products are fully compliant with REACH, RoHS, TSCA, and other regulatory requirements in the various regions where they are supplied.
Standard Certification
All SolarEdge products are designed with safety in mind, both at the individual component level and at the system level. We use advanced technology to protect users, site owners, installers, operations and maintenance staff and anyone who comes in contact with our products from potential safety risks.
The overall managerial responsibility for product safety at SolarEdge belongs to the SolarEdge executive product Safety Committee, which includes our VP R&D, VP Customer Service, VP Quality & Reliability, and VP General Counsel and Corporate Secretary. Product safety issues and risks are discussed by the Committee on a quarterly basis.
Each product safety incident or risk is examined by a combined team of our product, service, and R&D experts. This team works to determine the source of the hazard. Once the source is identified, corrective actions are set in place with adjustments to the relevant practices: installation training, product manuals, product physical design, product algorithms, monitoring systems or other safety features.
Due to the often-high voltage of PV systems, precautions must be taken to ensure the safety of people and avoid property damage. The SolarEdge PV systems adopt a holistic approach in reducing the risks associated with electrocution and fire by providing an integrated safety solution that combines enhanced protection and detection mechanisms.
As part of this holistic approach, we applied various safety mechanisms to our products and continue to apply new mechanisms based on our risk analysis process. Prominent examples of mechanisms already implemented to various extents in our products include:
Product Safety
Refurbishing
Product End-of-Life
Sustainable Packaging
Lifecycle Assessment
Standard Certification
Product Safety
Sustainability Report 2023 /
Safe & Sustainable Products
Join the SolarEdge Conversation
Contact our sustainability / ESG team
Contact us
How can we help you?
Reducing a PV system’s DC voltage to a safe level when the system is shut down
Designing for early fault detection
Applying active and continuous protection mechanisms
Supporting module-level monitoring with actionable fault alerts
Allowing conductors to rapidly discharge their electric load down to safe voltage levels
A key element of our integrated safety system is our SafeDC™ built-in proprietary safety technology. This feature is designed to minimize the risk of electrocution from high DC voltage. Upon activation of SafeDC™, our Power Optimizers automatically revert to their default touch-safe voltage of only 1V in less than one minute. SafeDC™ is activated in the following cases: during installation, when strings are disconnected from the inverter; when the inverter is turned off, locked or disabled; or when AC connection is shut down. The SafeDC™ feature helps to protect people engaged in PV system inspection and maintenance activities, as well as enabling emergency responders to address fires in homes or other buildings with confidence that the system does not pose an additional hazard.
Our monitoring abilities are another core part of our holistic safety management system. SolarEdge’s platform provides continuous remote monitoring at the module, string, and system level, allowing for greater visibility of system performance. The platform’s automatic alerts are designed to provide accurate and immediate fault detection, allowing for better hazard recognition and rapid response in case of product safety incidents.
An additional important safety feature of our systems is our advanced electric arc detection and prevention mechanism, already operated in many of our installed and monitored SolarEdge PV systems. An electric arc is an unintended, prolonged electrical discharge occurring across a small air gap. Since photovoltaic systems have many connection points, arc faults can occur, causing potential fire hazards. SolarEdge has developed state-of-the-art arc fault detection algorithms and AFCI (Arc Fault Circuit Interruption) mechanisms. These algorithms are designed to locate potential arc faults and to prevent them through corrective actions and are available for implementation on more than a million of our inverters. The algorithms were tested by certification entities and third-party companies to ensure that they pass the set requirements and provide the expected performance, under a full range of electrical conditions and various types of installations.
A prominent example of these mechanisms is the SolarEdge Sense Connect feature included in the new S-Series Power Optimizers. SolarEdge Sense Connect is an industry-first technology that detects temperature increase at the connector level, stopping power flow before an arc can occur.
We dedicate significant resources to widespread safety training, focusing on potential risks related to our business and products, such as electrification, fire and working on roofs. This training is conducted both for our employees (see “Health & Safety”) and our global community of installers (see “Customer Service”).
All SolarEdge products are designed with safety in mind, both at the individual component level and at the system level. We use advanced technology to protect users, site owners, installers, operations and maintenance staff and anyone who comes in contact with our products from potential safety risks.
The overall managerial responsibility for product safety at SolarEdge belongs to the SolarEdge executive product Safety Committee, which includes our VP R&D, VP Customer Service, VP Quality & Reliability, and VP General Counsel and Corporate Secretary. Product safety issues and risks are discussed by the Committee on a quarterly basis.
Each product safety incident or risk is examined by a combined team of our product, service, and R&D experts. This team works to determine the source of the hazard. Once the source is identified, corrective actions are set in place with adjustments to the relevant practices: installation training, product manuals, product physical design, product algorithms, monitoring systems or other safety features.
Due to the often-high voltage of PV systems, precautions must be taken to ensure the safety of people and avoid property damage. The SolarEdge PV systems adopt a holistic approach in reducing the risks associated with electrocution and fire by providing an integrated safety solution that combines enhanced protection and detection mechanisms.
As part of this holistic approach, we applied various safety mechanisms to our products and continue to apply new mechanisms based on our risk analysis process. Prominent examples of mechanisms already implemented to various extents in our products include:
Product Safety
In recent years, the packaging design process for new SolarEdge products focused on finding cost-effective packaging molds that could be made from recyclable materials while fully protecting our products from harm during shipment. Wherever such reasonable options were found, the company designed, and is now using, recyclable packaging materials such as cardboard, pulp and wood. Our Power Optimizers, batteries, and some additional products, are now delivered in packaging made from these recyclable materials. We continue to search for recyclable packaging options for our other products as well, striving to meet both physical and reasonable cost criteria. In parallel, we are monitoring evolving regulations on packaging materials in different global regions to ensure our current and future compliance.
Sustainable Packaging
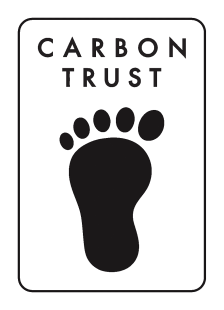
SolarEdge solutions support the worldwide transition to renewable, low-carbon power generation and consumption. The use of our systems allows for millions of tonnes of GHG emissions to be avoided each year. We also strive to examine and reduce the carbon emissions related to the sourcing, production and shipping of our products.
As part of these efforts, we conducted a comprehensive carbon footprint analysis for leading models of our inverters and Power Optimizers. The analysis process was led and certified by carbon footprint and decarbonization experts, Carbon Trust. The analysis allows us to understand the main emission sources throughout our products’ lifecycle, helping us better understand our emission reduction opportunities. We are currently working on the expansion of our LCA analysis scope for several additional products and additional environmental impacts and aim to complete this expanded process during 2024.
Lifecycle Assessment
Our products are built durably, for the long term and come with an extensive warranty. However, if one of our inverters or batteries nonetheless exhibits a malfunction that cannot be repaired on-site or remotely within the warranty period, it is replaced by the Company. SolarEdge inverters and batteries that need to be replaced are often sent to our refurbishing sites in Europe and the U.S. where Company refurbishing experts examine the malfunction, change electronic or other components as required, conduct quality tests (similar to those that new products are put through), and package the refurbished products as viable replacements. The refurbishing process and expertise provide both a cost-saving benefit for the company and a circularity environmental value. The process reduces some of the need for new electronic components, as well as the costs and environmental impact associated with shipping by partially reducing overseas delivery of new products. Malfunctioned products that cannot be refurbished, are often recycled (see “Product End-of-Life” below).
Refurbishing
We build our products for lasting performance, offering extensive warranties for Power Optimizers and inverters, so customers can benefit from highly efficient clean energy without wasting resources on replacement units. To further reduce waste and material usage, we also refurbish products - in cases where it is possible and viable (see “Refurbishing” above). We also work to ensure the recyclability of our products when they reach their eventual end-of-life stages. See full details in section “Waste Management”.
We help in securing a sustainable end-of-life for our products by participating in regulatory schemes mandated in some regions where we operate, in which manufacturers and importers of electronic equipment and batteries pay levies aimed to fund the eventual collection and recycling of their sold products, at their eventual end-of-life. Such schemes include the EU “Take Back” program of the Waste Electrical and Electronic Equipment (WEEE) directive, and other similar country-specific regulations.
We’ve instituted a useful procedure for waste recovery at some of our sites, including Sella 1 in Israel as an example. Non-household waste including hazardous waste, carboard, and scrap metal and e-waste is separated at the source and sent for external recycling at licensed facilities. This eases the later external process of recycling.
Recently, storage solutions have been forming an increasing part of SolarEdge’s activities, offerings and revenues. In parallel, the Company has experienced growing interest from stakeholders regarding the challenging global issues of battery end-of-life. In the cases of batteries that have experienced defaults, the batteries will often undergo a refurbishing process at SolarEdge designated sites (see above). These batteries can often be refurbished and reused (especially when the fault is an issue with electronic components). We began working with battery recycling sites in several locations in order to handle remaining batteries that cannot be repaired). We continue to examine potential approaches and solutions to mitigate this issue.
Product End-of-Life
At SolarEdge, safety is a primary feature of all our product offerings, and is a key element of our product design, development and testing. Similarly, as an industry leader in technologies that promote environmentally friendly solutions for energy generation, we strive to minimize the footprint of our value chain as much as possible.
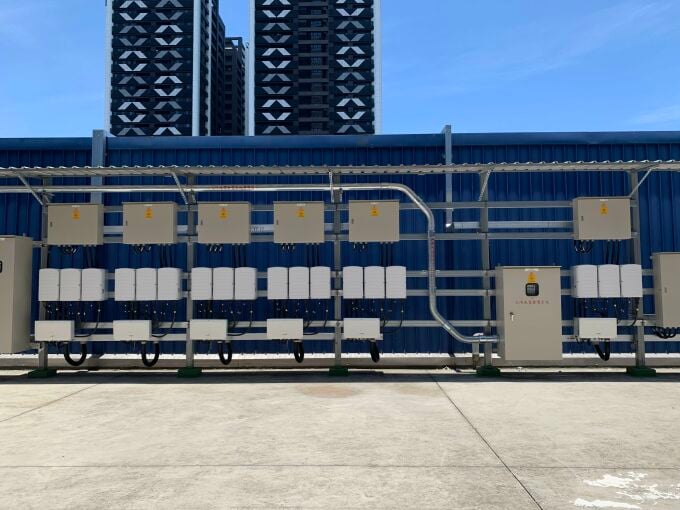
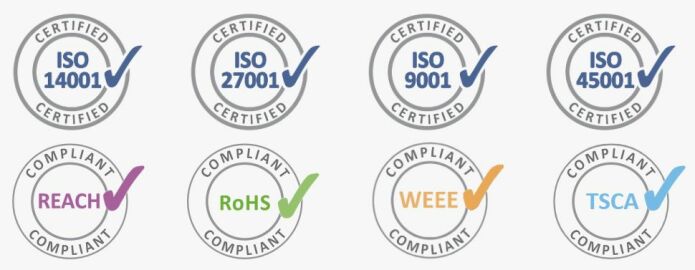
SolarEdge complies with the following international standards and with various environmental regulations:
We continuously act to certify all the manufacturing and R&D sites under our operational control according to relevant ISO standards for management systems in the fields of quality, environment and safety. By the end of 2023, 100% of the designated sites in all relevant countries (Israel, South-Korea, Italy and the US) were certified to ISO 9001 (quality), ISO 14001 (environmental management) and ISO 45001 (safety management).
All SolarEdge products are fully compliant with REACH, RoHS, TSCA, and other regulatory requirements in the various regions where they are supplied.
Standard Certification