Join the SolarEdge Conversation
Contact a product expert or sales representative
Contact us
How can we help you?
Environmental Compliance of our Operations
Solvent Purification and Reusage in Sella 2
Water Efficiency
Resource Efficiencies
at our Sella 1 Facility
Working to Reduce the GHG Emissions of our Operations
Sustainability Report 2022 /
Climate Change Mitigation & Resource Efficiency
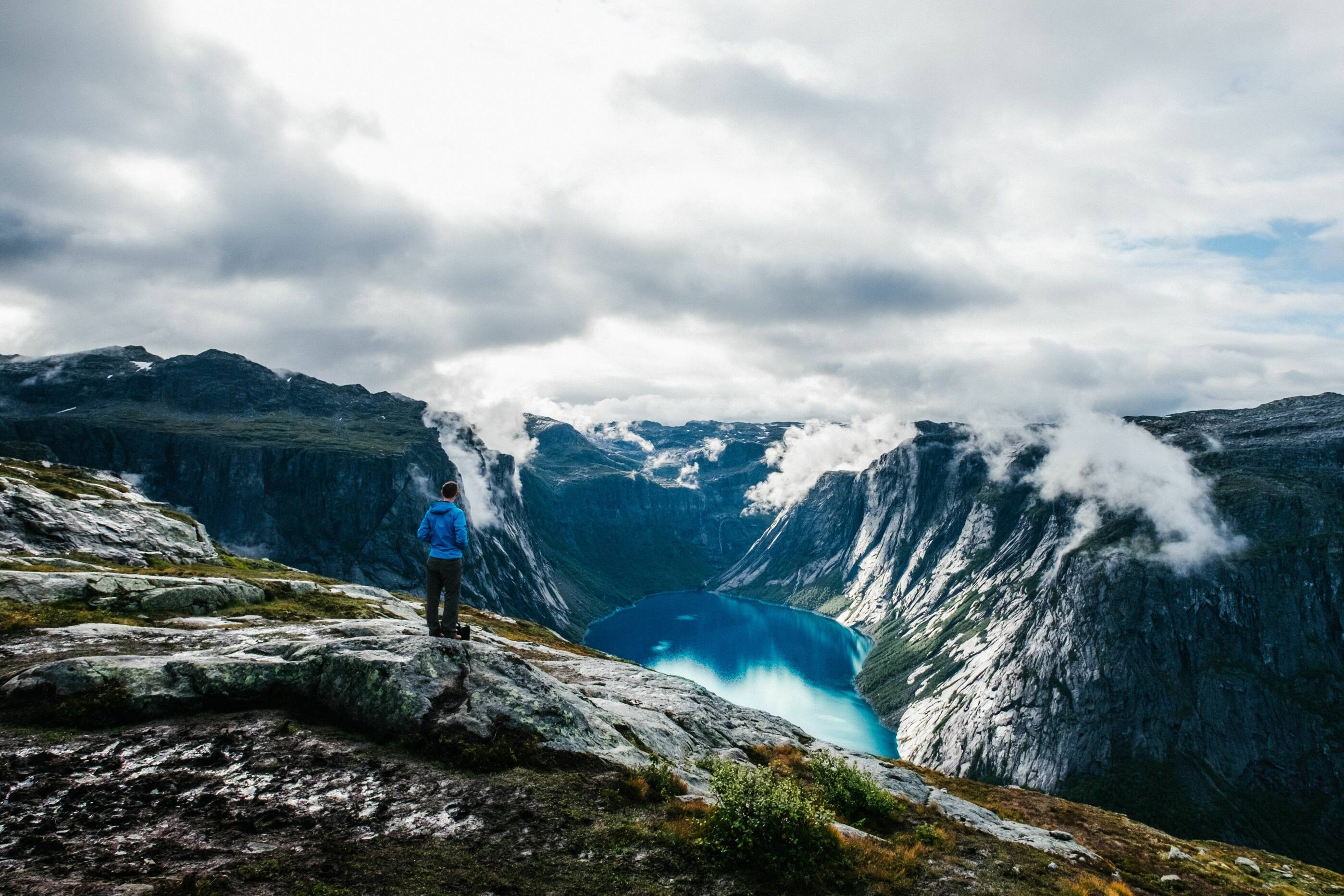
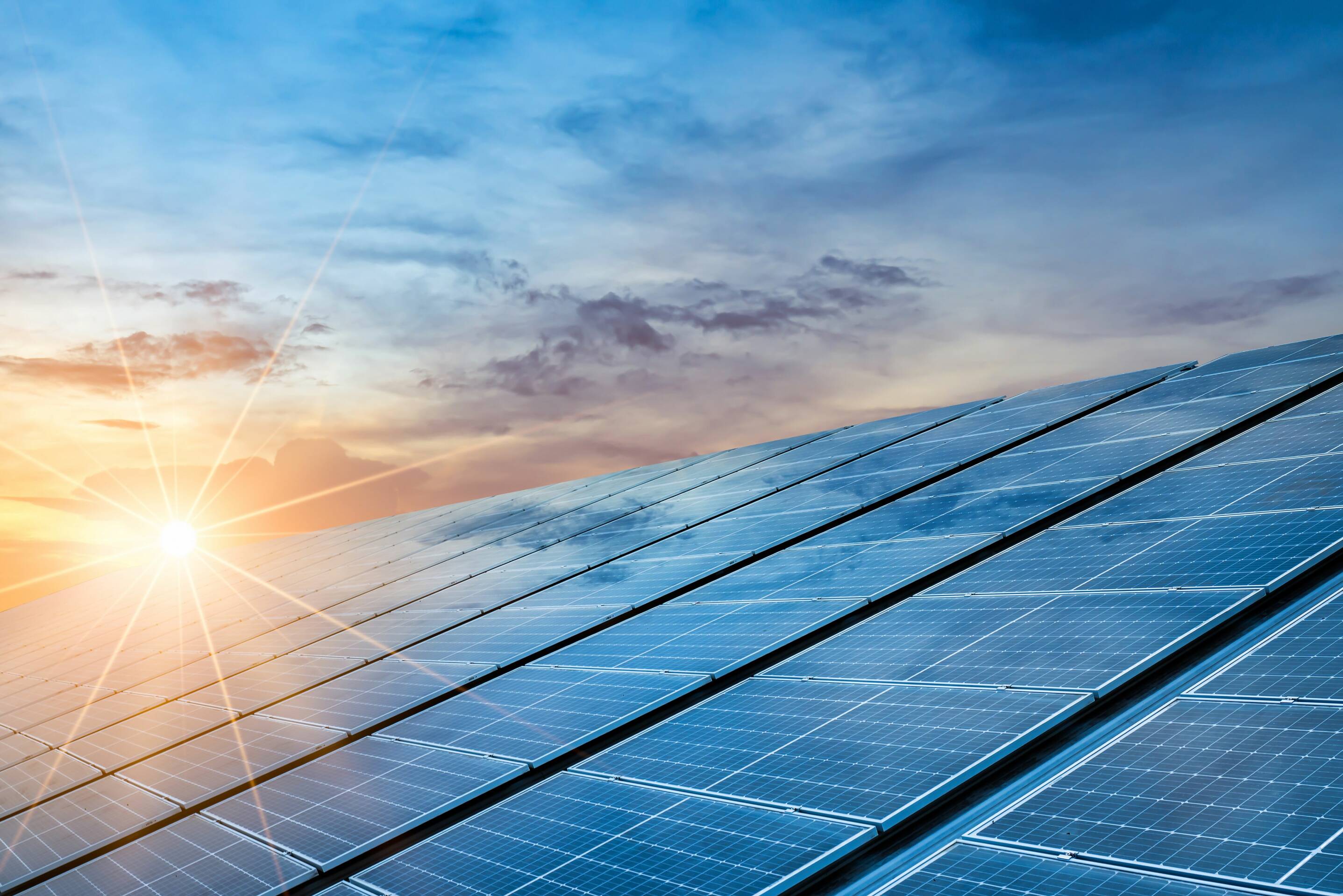
SolarEdge’s solutions contribute to the efforts to mitigate global climate change. Our renewable energy solutions reduce carbon emissions by millions of tonnes each year, enabling individuals, organizations, and governments to reduce their carbon footprint. Across our operations and in our supply chain, we continually seek to produce, distribute, deliver, and maintain our materials in ways that will minimize resource consumption and reduce environmental impact.
Almost all water used at SolarEdge’s operated sites is provided by municipal water supplies. Water from other sources is a negligible part (1%) of total water withdrawal.
In general, the activities at all SolarEdge sites and offices are not water intensive. A total of ~63,000 m3 withdrawn by our global operations in 2022 is equivalent to the estimated annual domestic consumption of approximately 800 people (based on average consumption in Israel)[1].
Nevertheless, we aim to conserve water wherever possible and use only what is strictly needed to support our teams in our global sites and offices. In several of our locations, we conserve water through water-saving devices on faucets and showers, and low-water flush mechanisms in our bathrooms, and leak detection systems.
Our Sella 1 production site in Israel excels in water efficiency and recycling. The primary water on-site usage is for the washing of residual coating and solder flux. This de-ionized water is maintained in a closed cycle which is entirely separate from the site’s wastewater system. The excess water from the process is re-treated and is almost entirely reused, with only small amounts of evaporated water being unretrievable. In 2022, over 6000 m3 of water were reused in this manner at Sella 1.
The Sella 2 site, which opened in 2022 and is currently in its ramp-up phase, is also highly efficient in water usage patterns. The site implemented a coolant circulation system that allows for almost all water used in its cooling tower to be reused through thousands of repeated process cycles each year, greatly diminishing the quantity of any related wastewater.
Overall, around 20% of our entire global water consumption is composed of internally recycled/reused water.
Water Efficiency
We are taking several steps and continue to search for additional reduction opportunities to allow us to progress towards our target:
We installed SolarEdge PV systems on the rooftops of three Company sites (Sella 1 and our headquarters in Herzliya in Israel, and Milpitas in the U.S), partially replacing fossil-fuel based external electricity. The installed three systems have a combined capacity of approximately 1 MWp. In 2023, we aim to install new SolarEdge PV systems on the roofs of three additional sites: Sella 2 (Korea), Umbertide (Italy), and our offices in London (U.K.). Additional sites are also being examined for potential PV system installation.
We have recently implemented an innovative electricity savings method in the new Sella 2 site. The production process of lithium-ion batteries involves using significant amounts of electricity in the charge/discharge cycles of battery formation. The technical limitations of the traditional battery production process often cause this electricity to be discharged without reusage. In contrast, the new method planned for Sella 2 production is designed to use an innovative electricity reservoir, allowing for an estimated 50% of the discharged electricity to be reused.
In May 2022, our Sella 1 manufacturing site in Israel transitioned to purchasing all of its external electricity needs from a recently opened private power plant. This private power plant produces its electricity using a highly efficient process that employs natural gas exclusively for combustion. It has a significantly improved carbon intensity compared to the general grid electricity in Israel, which still includes partial combustion of coal. The related Scope 2 emission reduction has, therefore, partially commenced in 2022, with full-year realization expected in 2023.
Our R&D facility at Modiin has installed smart energy-saving systems, such as motion detectors, which allow AC and lighting systems to use less power when not in use.
To complement the previous steps, we are examining additional opportunities for integrating renewable energy in other areas of our operations.
Despite these efforts, our 2022 emission intensity increased to 13.53 tonnes CO2e/$M revenue, compared to 13.39 tonnes CO2e/$M revenue in 2021 (an increase of 1%). However, the 2022 emission intensity was still lower by 5% compared with the 2020 base year. Our absolute Scope 1+2 emissions rose by 60% in 2022 compared to 2021, while revenues also increased significantly, at a similar rate (by 58%). The vast majority of the 2022 increase in our emissions was related to electricity and natural gas consumption at the newly opened Sella 2 site in Korea. Even with the innovative electricity saving method described above for Sella 2, battery production is generally more energy intense than the manufacturing of our solar products. Also, since the site is still in its ramp-up phase, some of its energy consumption is yet to be reflected in increased revenues. Therefore, the overall intensity (emission per revenue) has increased. If excluding the Sella 2 ramp-up activities, the Scope 1+2 emission-per-revenue has decreased in 2022 by 33% compared with 2021.
We will consider updating and/or rebaselining our emission targets moving forward, to better reflect our significantly expanded operations.
As part of our commitment to minimize negative environmental impact, we have set a greenhouse gas (GHG) emission intensity reduction target. Our current target is to achieve a 30% reduction in total Scope 1+2 GHG emissions per million $ revenue by 2025, compared to that of 2020.
Working to Reduce the GHG Emissions of our Operations
Our Sella 2 site in South-Korea uses NMP (N-Methyl-2-Pyrrolidone) as a solvent for lithium-ion battery cell production. The site has set up an efficient NMP purification system, which allows to purify and reuse approximately 90% of the NMP material.
This system significantly reduces the need to send NMP for external purification and/or to hazardous waste treatment. This results in greater resource efficiency, and an overall reduced environmental impact.
Solvent Purification and Reusage in Sella 2
We fully comply with all environmental (and other) regulations that apply in all regions where we operate. To date, SolarEdge has not experienced a single environmental incident that resulted in any retaliatory steps from regulators in any country. We have not been subject to any fines, penalties or sanctions related to environmental regulations.
Environmental Compliance of our Operations
New and highly efficient machinery such as chillers, air blowers, air treatment systems and lighting, all designed to achieve high usage efficiencies and minimize energy consumption.
Site personnel engagement in continuous monitoring and control of site conditions and change of external climate to adjust the operating terms accordingly and preserve energy. For example, recent improvements were made to the site’s heating, ventilation and air-conditioning (HVAC) operation system algorithm which enabled the reduction of about one third of its previous energy consumption.
Establishment of an automatic shut-down routine for AC and lightning for weekends, when the site is not operating.
The site uses a mixed bed resin system for water deionization (prior to usage in the production process). This system was designed to allow almost all water consumed to be reused in the process. Further details below.
The recent optimization of the water deionization process parameters has significantly reduced the frequency of required resin replacement.
The output process water cleaning system was also recently improved with a new precipitation tank installed upstream to the system’s filters. The improved process has enabled a significant reduction of required filter replacements.
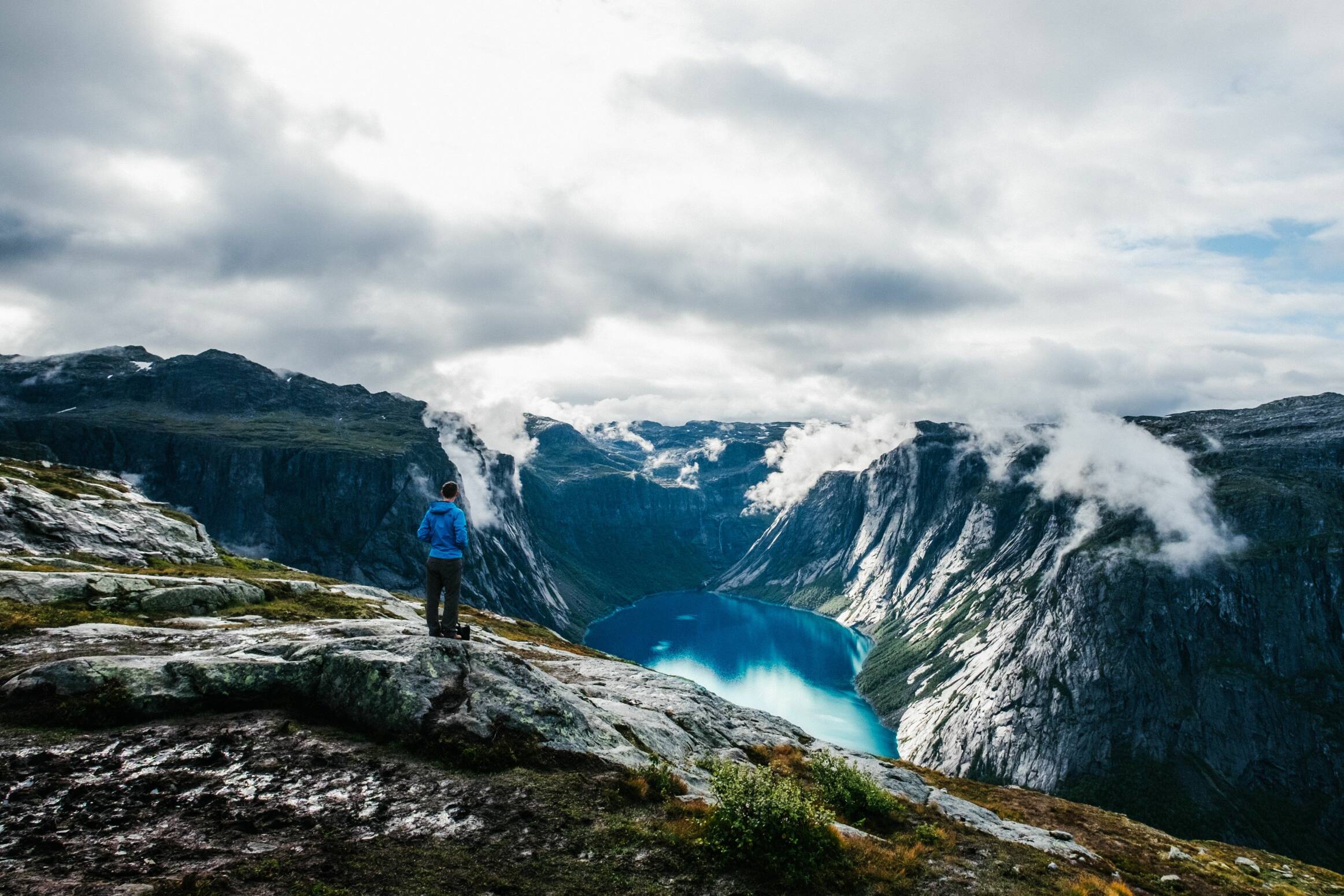
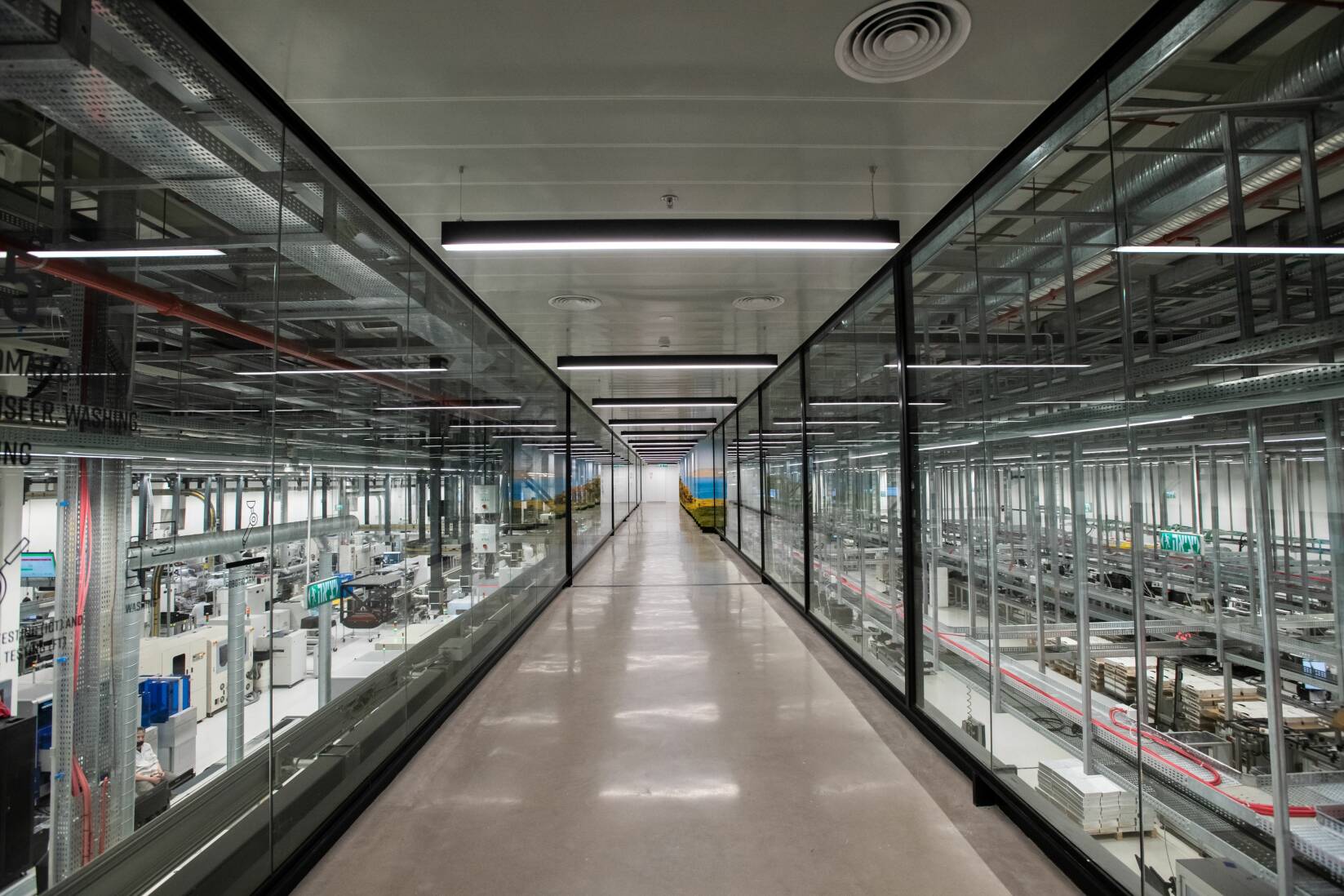
Our Sella 1 manufacturing site in Israel began full operation in 2021. The site was designed to operate at high levels of energy and resource efficiency, with continuous improvements facilitated though advanced operation and monitoring systems. Existing and newly improved features include:
Resource Efficiencies at our Sella 1 Facility
We fully comply with all environmental (and other) regulations that apply in all regions where we operate. To date, SolarEdge has not experienced a single environmental incident that resulted in any retaliatory steps from regulators in any country. We have not been subject to any fines, penalties or sanctions related to environmental regulations.
Environmental Compliance of our Operations
[1]
Source: Mei-Avivim water corporation- Average annual water consumption per person in Israel in ~80 m3.
Join the SolarEdge Conversation
Contact a product expert or sales representative
Contact us
How can we help you?
Our Sella 2 site in South-Korea uses NMP (N-Methyl-2-Pyrrolidone) as a solvent for lithium-ion battery cell production. The site has set up an efficient NMP purification system, which allows to purify and reuse approximately 90% of the NMP material.
This system significantly reduces the need to send NMP for external purification and/or to hazardous waste treatment. This results in greater resource efficiency, and an overall reduced environmental impact.
Solvent Purification and Reusage in Sella 2
Despite these efforts, our 2022 emission intensity increased to 13.53 tonnes CO2e/$M revenue, compared to 13.39 tonnes CO2e/$M revenue in 2021 (an increase of 1%). However, the 2022 emission intensity was still lower by 5% compared with the 2020 base year. Our absolute Scope 1+2 emissions rose by 60% in 2022 compared to 2021, while revenues also increased significantly, at a similar rate (by 58%). The vast majority of the 2022 increase in our emissions was related to electricity and natural gas consumption at the newly opened Sella 2 site in Korea. Even with the innovative electricity saving method described above for Sella 2, battery production is generally more energy intense than the manufacturing of our solar products. Also, since the site is still in its ramp-up phase, some of its energy consumption is yet to be reflected in increased revenues. Therefore, the overall intensity (emission per revenue) has increased. If excluding the Sella 2 ramp-up activities, the Scope 1+2 emission-per-revenue has decreased in 2022 by 33% compared with 2021.
We will consider updating and/or rebaselining our emission targets moving forward, to better reflect our significantly expanded operations.
We are taking several steps and continue to search for additional reduction opportunities to allow us to progress towards our target:
We installed SolarEdge PV systems on the rooftops of three Company sites (Sella 1 and our headquarters in Herzliya in Israel, and Milpitas in the U.S), partially replacing fossil-fuel based external electricity. The installed three systems have a combined capacity of approximately 1 MWp. In 2023, we aim to install new SolarEdge PV systems on the roofs of three additional sites: Sella 2 (Korea), Umbertide (Italy), and our offices in London (U.K.). Additional sites are also being examined for potential PV system installation.
We have recently implemented an innovative electricity savings method in the new Sella 2 site. The production process of lithium-ion batteries involves using significant amounts of electricity in the charge/discharge cycles of battery formation. The technical limitations of the traditional battery production process often cause this electricity to be discharged without reusage. In contrast, the new method planned for Sella 2 production is designed to use an innovative electricity reservoir, allowing for an estimated 50% of the discharged electricity to be reused.
In May 2022, our Sella 1 manufacturing site in Israel transitioned to purchasing all of its external electricity needs from a recently opened private power plant. This private power plant produces its electricity using a highly efficient process that employs natural gas exclusively for combustion. It has a significantly improved carbon intensity compared to the general grid electricity in Israel, which still includes partial combustion of coal. The related Scope 2 emission reduction has, therefore, partially commenced in 2022, with full-year realization expected in 2023.
Our R&D facility at Modiin has installed smart energy-saving systems, such as motion detectors, which allow AC and lighting systems to use less power when not in use.
To complement the previous steps, we are examining additional opportunities for integrating renewable energy in other areas of our operations.
As part of our commitment to minimize negative environmental impact, we have set a greenhouse gas (GHG) emission intensity reduction target. Our current target is to achieve a 30% reduction in total Scope 1+2 GHG emissions per million $ revenue by 2025, compared to that of 2020.
Working to Reduce the GHG Emissions of our Operations
Resource Efficiencies at our Sella 1 Facility
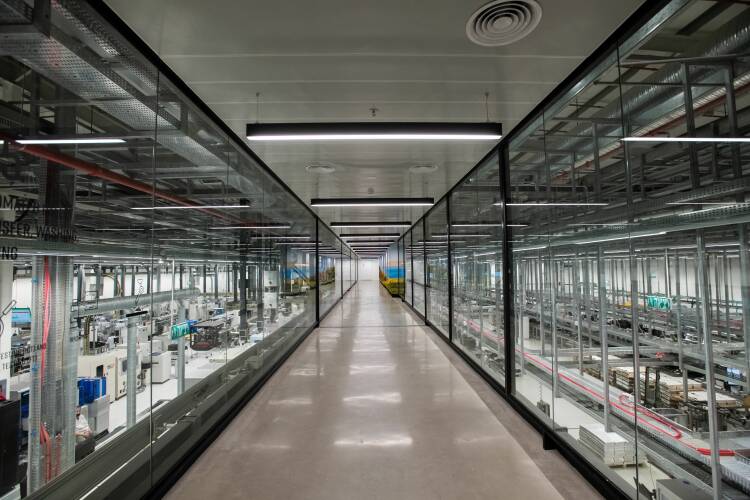
New and highly efficient machinery such as chillers, air blowers, air treatment systems and lighting, all designed to achieve high usage efficiencies and minimize energy consumption.
Site personnel engagement in continuous monitoring and control of site conditions and change of external climate to adjust the operating terms accordingly and preserve energy. For example, recent improvements were made to the site’s heating, ventilation and air-conditioning (HVAC) operation system algorithm which enabled the reduction of about one third of its previous energy consumption.
Establishment of an automatic shut-down routine for AC and lightning for weekends, when the site is not operating.
The site uses a mixed bed resin system for water deionization (prior to usage in the production process). This system was designed to allow almost all water consumed to be reused in the process. Further details below.
The recent optimization of the water deionization process parameters has significantly reduced the frequency of required resin replacement.
The output process water cleaning system was also recently improved with a new precipitation tank installed upstream to the system’s filters. The improved process has enabled a significant reduction of required filter replacements.
Our Sella 1 manufacturing site in Israel began full operation in 2021. The site was designed to operate at high levels of energy and resource efficiency, with continuous improvements facilitated though advanced operation and monitoring systems. Existing and newly improved features include:
Almost all water used at SolarEdge’s operated sites is provided by municipal water supplies. Water from other sources is a negligible part (1%) of total water withdrawal.
In general, the activities at all SolarEdge sites and offices are not water intensive. A total of ~63,000 m3 withdrawn by our global operations in 2022 is equivalent to the estimated annual domestic consumption of approximately 800 people (based on average consumption in Israel)[1].
Nevertheless, we aim to conserve water wherever possible and use only what is strictly needed to support our teams in our global sites and offices. In several of our locations, we conserve water through water-saving devices on faucets and showers, and low-water flush mechanisms in our bathrooms, and leak detection systems.
Our Sella 1 production site in Israel excels in water efficiency and recycling. The primary water on-site usage is for the washing of residual coating and solder flux. This de-ionized water is maintained in a closed cycle which is entirely separate from the site’s wastewater system. The excess water from the process is re-treated and is almost entirely reused, with only small amounts of evaporated water being unretrievable. In 2022, over 6000 m3 of water were reused in this manner at Sella 1.
The Sella 2 site, which opened in 2022 and is currently in its ramp-up phase, is also highly efficient in water usage patterns. The site implemented a coolant circulation system that allows for almost all water used in its cooling tower to be reused through thousands of repeated process cycles each year, greatly diminishing the quantity of any related wastewater.
Overall, around 20% of our entire global water consumption is composed of internally recycled/reused water.
Water Efficiency
SolarEdge’s solutions contribute to the efforts to mitigate global climate change. Our renewable energy solutions reduce carbon emissions by millions of tonnes each year, enabling individuals, organizations, and governments to reduce their carbon footprint. Across our operations and in our supply chain, we continually seek to produce, distribute, deliver, and maintain our materials in ways that will minimize resource consumption and reduce environmental impact.
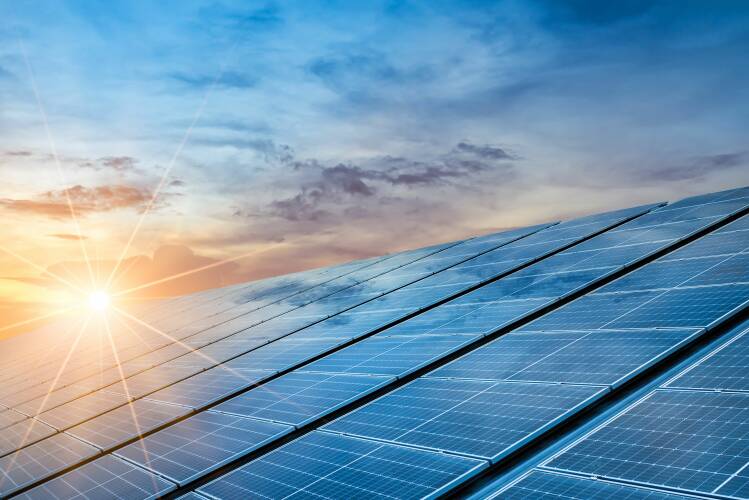