An increase in the share of operational roles in the Company’s workforce in 2022, with the significant expansion of our own manufacturing sites;
The significant expansion of our in-house safety workforce in late 2021 and early 2022 which resulted in an improved safety reporting culture, with enhanced internal transparency and better incident tracking.
The overall TRIR (rate of recordable injuries) of our global company employees in 2022 was 0.60. This represents a 22% increase compared to the 2021 TRIR (0.50), although this still achieves our continuous target of an annual TRIR rate no greater than 0.7.
In parallel, the LTIR (rate of lost days due to safety incidents) of our global company has slightly improved, dropping from 11.9 in 2021 to 11.0 in 2022 (-8%).
Our analysis of the safety figures indicates two likely reasons for the increase in TRIR in 2022:
Sustainability Report 2022 /
Health & Safety
LTIR Rate - Global Company Employees
15.0
60
11.9
11.0
2022
2021
2020
TRIR Rate - Global Company Employees
0.66
60
0.50
0.61
2022
2021
2020
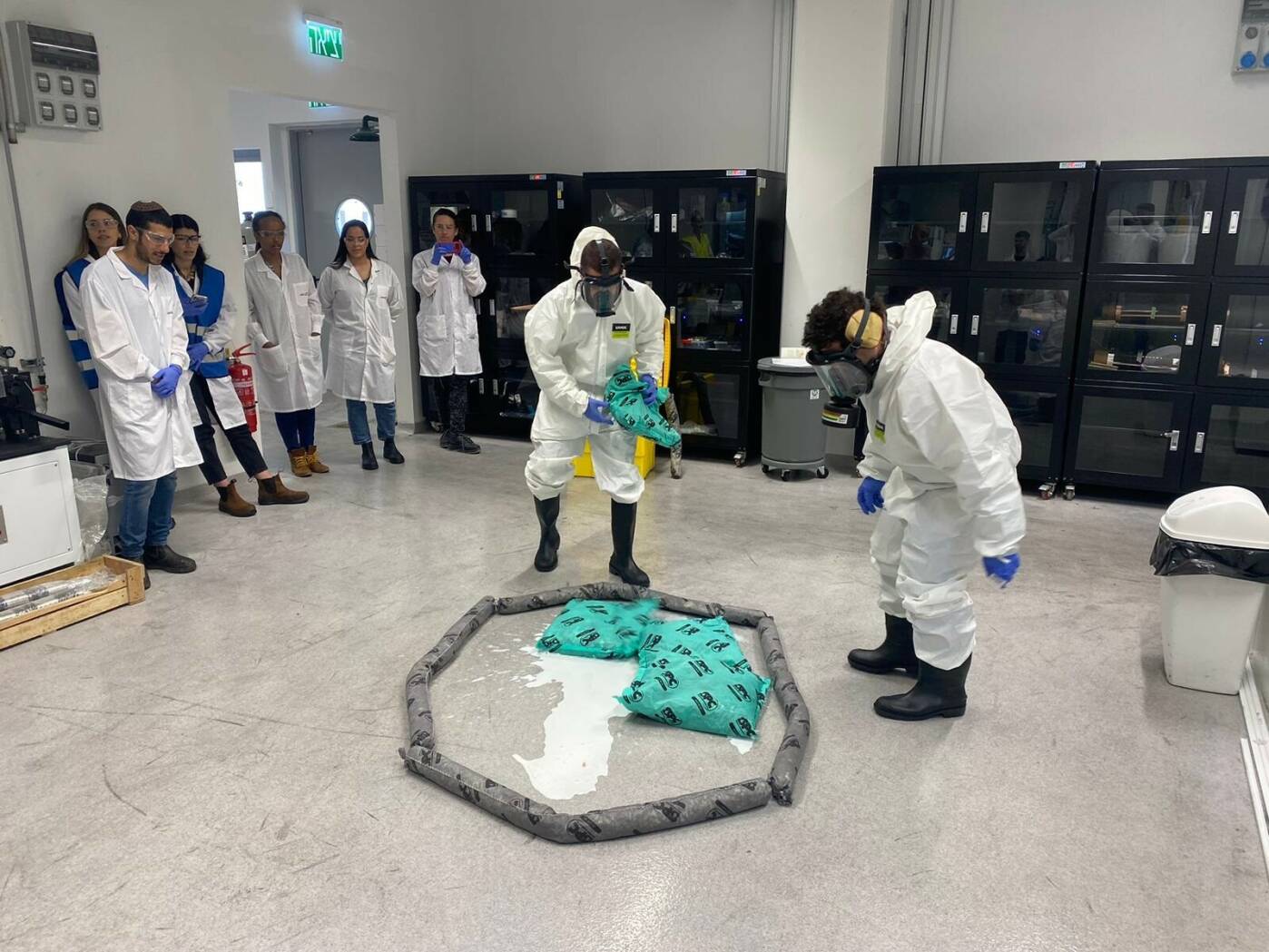
hours of safety training,
which total an average of over
4.6
22,800
annual training hours
per global employee.
In 2022, SolarEdge employees participated in more than
An EHS regulatory and compliance monitoring system, tracking relevant global regulations, and assisting with customized audit planning;
An incident reporting and investigation system for our Israeli sites, aimed at methodically finding the incident’s root cause and helping with risk elimination; and
Training management to better track training obligations and the progress of our expanding global workforce.
Safety training was significantly expanded at SolarEdge in 2022. The expanded training components included enhanced fire prevention and emergency handling (specifically focusing on the Li-Ion battery risks), more comprehensive first aid training, and new mandatory annual on-line safety training for all employees.
In addition, we also implemented new systems in 2022 for tracking global EHS performance, aimed to help reduce safety risks and support ongoing EHS compliance worldwide. These systems include:
Our safety practices include:
Nominated Safety Officers at each company manufacturing/R&D site. Our Safety Officers have gained specific expertise in the processes and technologies that characterize SolarEdge’s activities.
Nominated lab electricity supervising engineers in two main R&D sites, focusing specifically on prevention of electricity-related incidents
Appointed and trained employees in each manufacturing/R&D site as Safety Trustees who help enhance their site’s local safety culture
Mandatory annual safety training for all employees
Mandatory job-specific training (such as proper use of protective equipment, working with high voltage, working in heights, safe use of machinery/chemicals/materials, etc.) for all employees in relevant roles
Comprehensive safety, fire, and emergency drill programs to ensure employees are well-versed with emergency procedures
Root-cause assessments of incidents and corrective actions
Conducting periodic internal and external EHS audits within the company and at contract manufacturer sites
Supplying employees with all necessary PPE (Personal Protective Equipment) according to the identified job-specific risks and all relevant regulations
Maintaining a healthy and ergonomic work environment. Provide employees with specialized ergonomic equipment when reasonably required/requested.
Safety performance: Overall accountability for safety at SolarEdge rests with the Vice President of Quality & Reliability (Q&R), a member of our executive management team. The SolarEdge Global EHS Director reports to the VP Q&R and manages all aspects of safety and environmental compliance and improvement. Safety performance is reported monthly to the company Chief Executive Officer and executive management, including specific safety incidents analysis, findings, corrective actions and updates on safety improvements.
We believe that all accidents and injuries at work are preventable, and we strive to achieve a zero-injury culture across our offices and operations. We comply with applicable occupational health and safety regulations. All SolarEdge manufacturing and R&D sites are certified to Occupational Health and Safety Quality Management Standard ISO 45001:2018.
Join the SolarEdge Conversation
Contact a product expert or sales representative
Contact us
How can we help you?
Join the SolarEdge Conversation
Contact a product expert or sales representative
Contact us
How can we help you?
4.6
annual training hours
per global employee.
hours of safety training,
which total an average of over
22,800
In 2022, SolarEdge employees participated in more than
An EHS regulatory and compliance monitoring system, tracking relevant global regulations, and assisting with customized audit planning;
An incident reporting and investigation system for our Israeli sites, aimed at methodically finding the incident’s root cause and helping with risk elimination; and
Training management to better track training obligations and the progress of our expanding global workforce.
Safety training was significantly expanded at SolarEdge in 2022. The expanded training components included enhanced fire prevention and emergency handling (specifically focusing on the Li-Ion battery risks), more comprehensive first aid training, and new mandatory annual on-line safety training for all employees.
In addition, we also implemented new systems in 2022 for tracking global EHS performance, aimed to help reduce safety risks and support ongoing EHS compliance worldwide. These systems include:
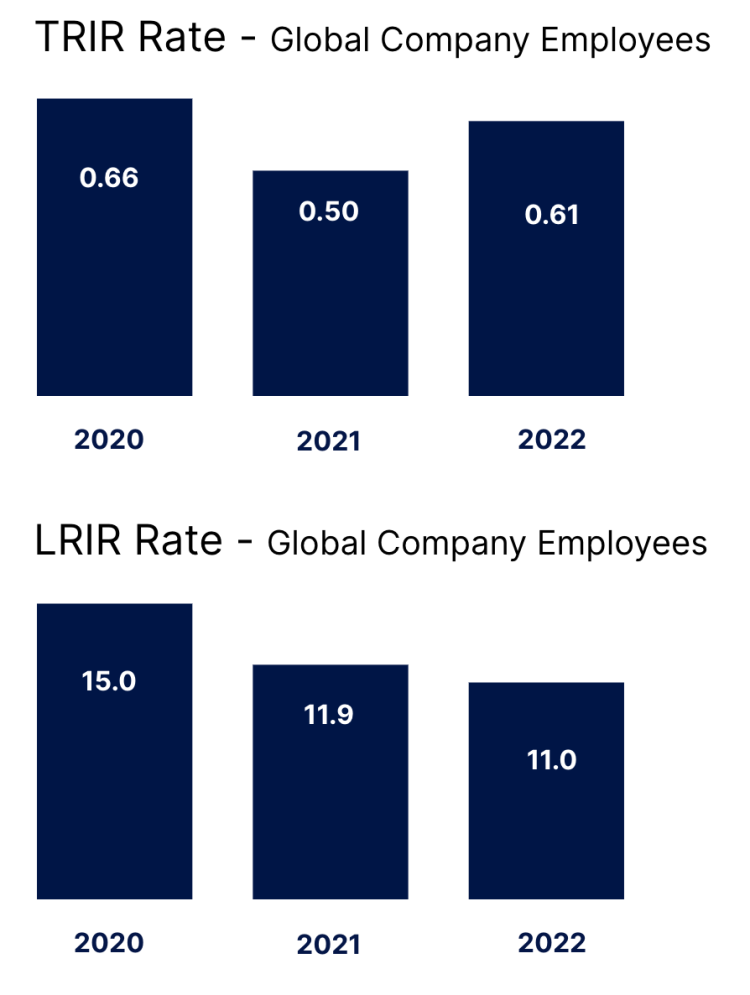
An increase in the share of operational roles in the Company’s workforce in 2022, with the significant expansion of our own manufacturing sites;
The significant expansion of our in-house safety workforce in late 2021 and early 2022 which resulted in an improved safety reporting culture, with enhanced internal transparency and better incident tracking.
The overall TRIR (rate of recordable injuries) of our global company employees in 2022 was 0.60. This represents a 22% increase compared to the 2021 TRIR (0.50), although this still achieves our continuous target of an annual TRIR rate no greater than 0.7.
In parallel, the LTIR (rate of lost days due to safety incidents) of our global company has slightly improved, dropping from 11.9 in 2021 to 11.0 in 2022 (-8%).
Our analysis of the safety figures indicates two likely reasons for the increase in TRIR in 2022:
Nominated Safety Officers at each company manufacturing/R&D site. Our Safety Officers have gained specific expertise in the processes and technologies that characterize SolarEdge’s activities.
Nominated lab electricity supervising engineers in two main R&D sites, focusing specifically on prevention of electricity-related incidents
Appointed and trained employees in each manufacturing/R&D site as Safety Trustees who help enhance their site’s local safety culture
Mandatory annual safety training for all employees
Mandatory job-specific training (such as proper use of protective equipment, working with high voltage, working in heights, safe use of machinery/chemicals/materials, etc.) for all employees in relevant roles
Comprehensive safety, fire, and emergency drill programs to ensure employees are well-versed with emergency procedures
Root-cause assessments of incidents and corrective actions
Conducting periodic internal and external EHS audits within the company and at contract manufacturer sites
Supplying employees with all necessary PPE (Personal Protective Equipment) according to the identified job-specific risks and all relevant regulations
Maintaining a healthy and ergonomic work environment. Provide employees with specialized ergonomic equipment when reasonably required/requested.
Our safety practices include:
Safety performance: Overall accountability for safety at SolarEdge rests with the Vice President of Quality & Reliability (Q&R), a member of our executive management team. The SolarEdge Global EHS Director reports to the VP Q&R and manages all aspects of safety and environmental compliance and improvement. Safety performance is reported monthly to the company Chief Executive Officer and executive management, including specific safety incidents analysis, findings, corrective actions and updates on safety improvements.
We believe that all accidents and injuries at work are preventable, and we strive to achieve a zero-injury culture across our offices and operations. We comply with applicable occupational health and safety regulations. All SolarEdge manufacturing and R&D sites are certified to Occupational Health and Safety Quality Management Standard ISO 45001:2018.